インタビュー
サステナブルなサプライチェーン実現への取り組み~花王株式会社
2024年7月10日
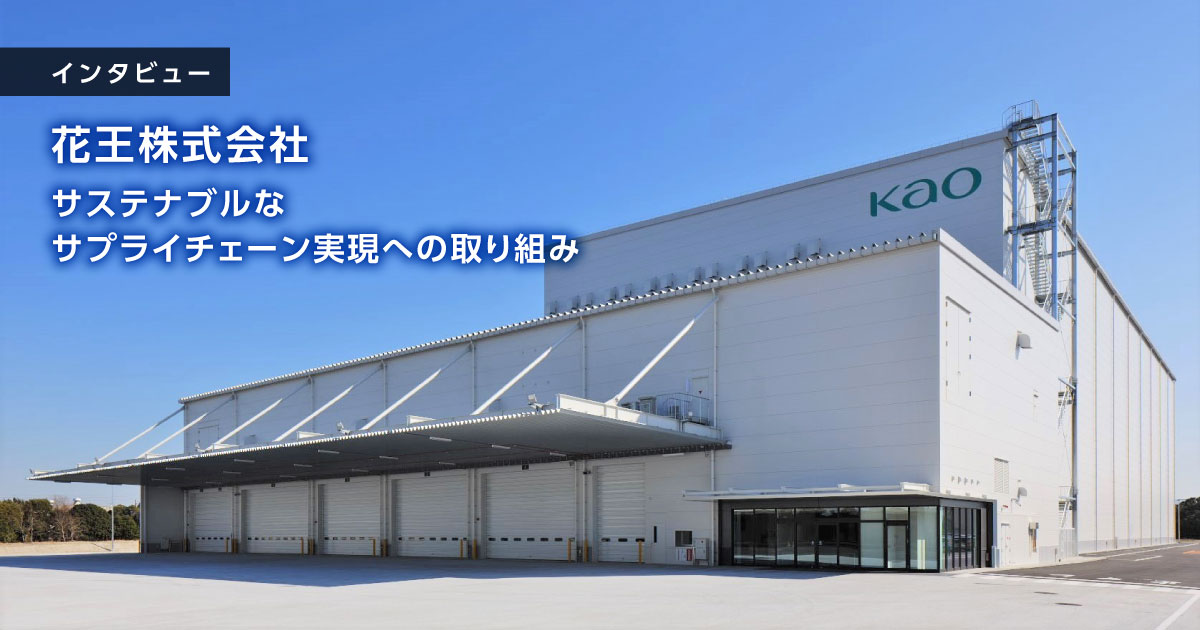
2023年3月より、花王株式会社は豊橋工場において次世代新倉庫の運用を開始しています。サステナブルなサプライチェーン構築を目指している花王SCM部門の徳山 尚昭様と青木 潤様に、同社のサプライチェーンへの取り組みについてお話を伺いました。
豊橋工場の次世代新倉庫は、少量多品種製品の生産に柔軟に対応し、物流作業の完全自動化と、隣接する工場および物流拠点との一体運営や、トラックによる入出荷の効率化を実現する、これまでにない拠点です。この中で、トラックの待機時間削減など場内におけるトラック運行のスマート化の取り組みにおいて、当社の「車両ナンバー認証システム」を導入いただきました。
目次
プロフィール
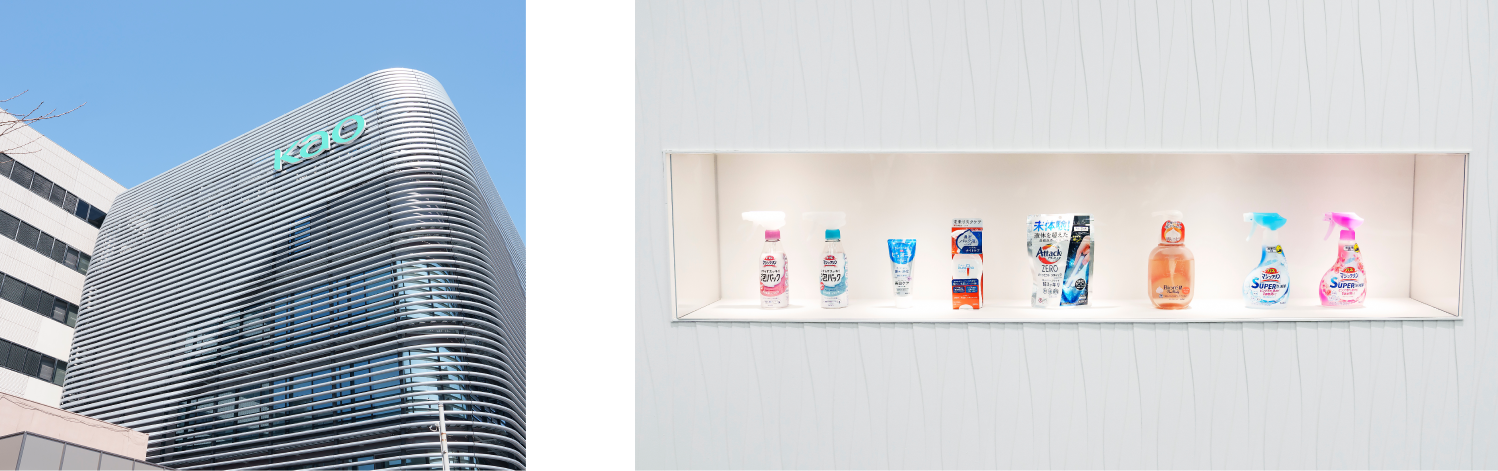
今回訪問した「すみだ事業所」(東京都墨田区)は、2023年8月に創業100周年を迎えた花王グループで最も長い歴史を持つ事業場で、研究開発・事業・サプライチェーン・管理部門等が集結しています。生活者に近い立地を活かし、価値を創造する環境の整備も進めながら、人と社会と地球にやさしいモノづくりを推進しています。
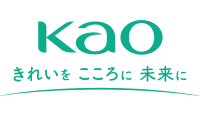
※記載の法人・団体名・組織名・所属・肩書きなどは、すべて取材時点でのものです。
本日はよろしくお願いします。
はじめに、お二人が所属するSCM(サプライチェーンマネジメント)部門や業務内容についてお聞かせください。
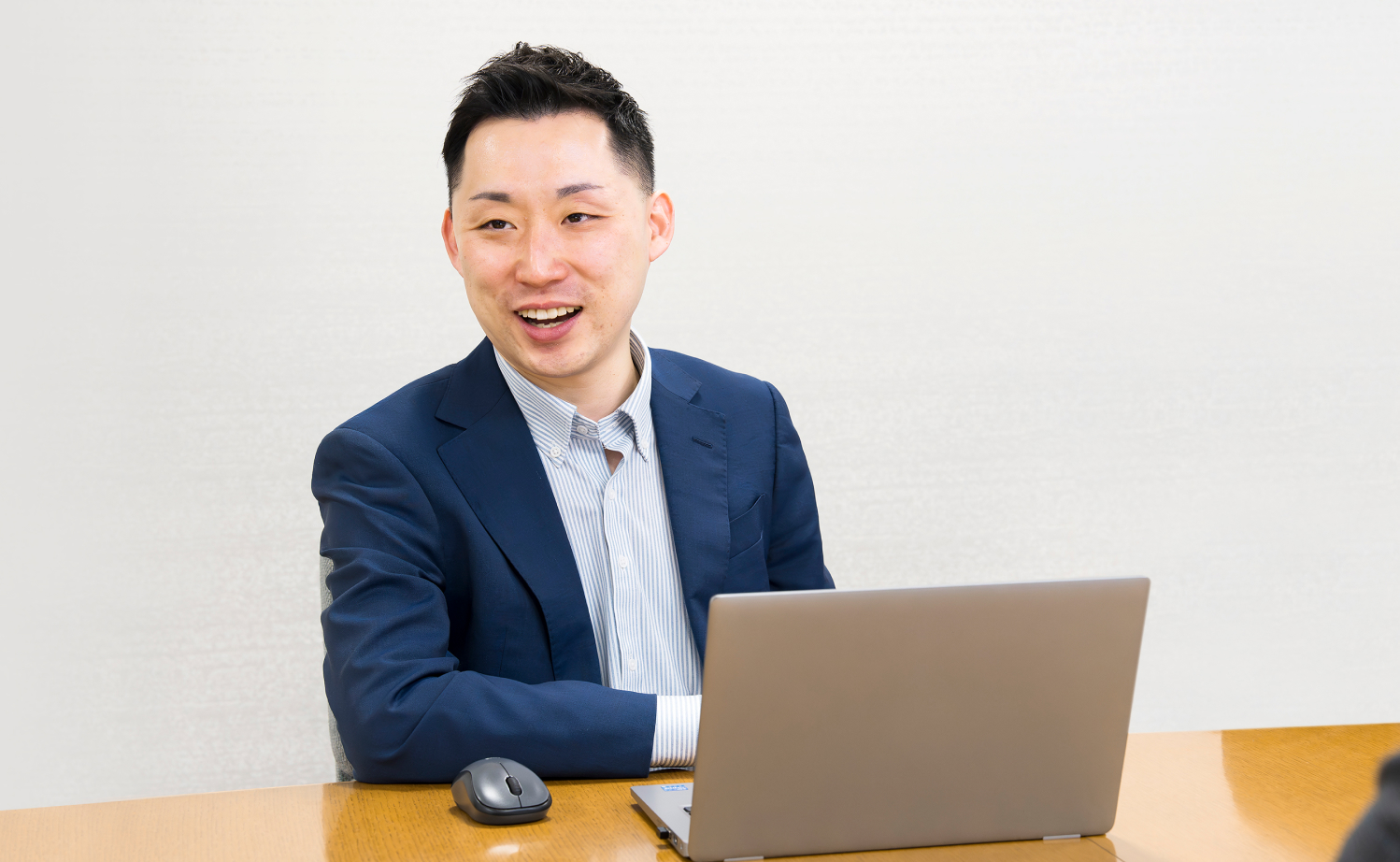
徳山 私はSCM部門の「ロジスティクスセンター」に所属しています。ロジスティクスセンターでは国内物流拠点の設計、戦略、企画を一手に担っており、その中の「ロジスティクス改革部」で、豊橋工場の次世代新倉庫をはじめとした、今後の物流システムや各拠点における、サステナブルを念頭においたソリューションの導入や、物流2024年問題対応などの計画立案に携わっています。
青木
私はSCM部門の「デジタルイノベーションプロジェクト」に所属しています。2021年7月に発足した、デジタルトランスフォーメーション(以下DX)を力強く推進する組織で、最新のIT技術やデータを使った業務改善やオペレーションの効率化を検討しています。そのひとつが豊橋工場の次世代倉庫建設プロジェクトで、新しい仕組みを共創するメンバーとしてプロジェクトに参画し、その中の取り組みにおいてJVCケンウッド・公共産業システム(以下JKPI)に協力いただきました。
デジタルイノベーションプロジェクトは、ビジネス力、データサイエンス力、データエンジニア力のそれぞれの強みを持った「データサイエンティスト」で構成され、メンバーはさまざまな部署のプロジェクトに参画しています。私もその一員として豊橋工場の次世代倉庫建設プロジェクトへの参画をしておりました。
モーダルシフトや共同輸送で物流2024年問題へ対応
まずは、花王様のサプライチェーンにおける、物流2024年問題への取り組みをお聞かせください。
徳山 花王は生産工場から卸へ配送する「メーカー物流」に加え、小売店まで配送する「卸物流」を弊社グループの物流会社で運用管理しています。輸送量も多いため、物流2024年問題は重要な社会的課題であり、輸送能力の不足などこれから起こる可能性のある問題に対して、ホワイト物流推進の活動を行っています。その中で2つほど事例を紹介します。
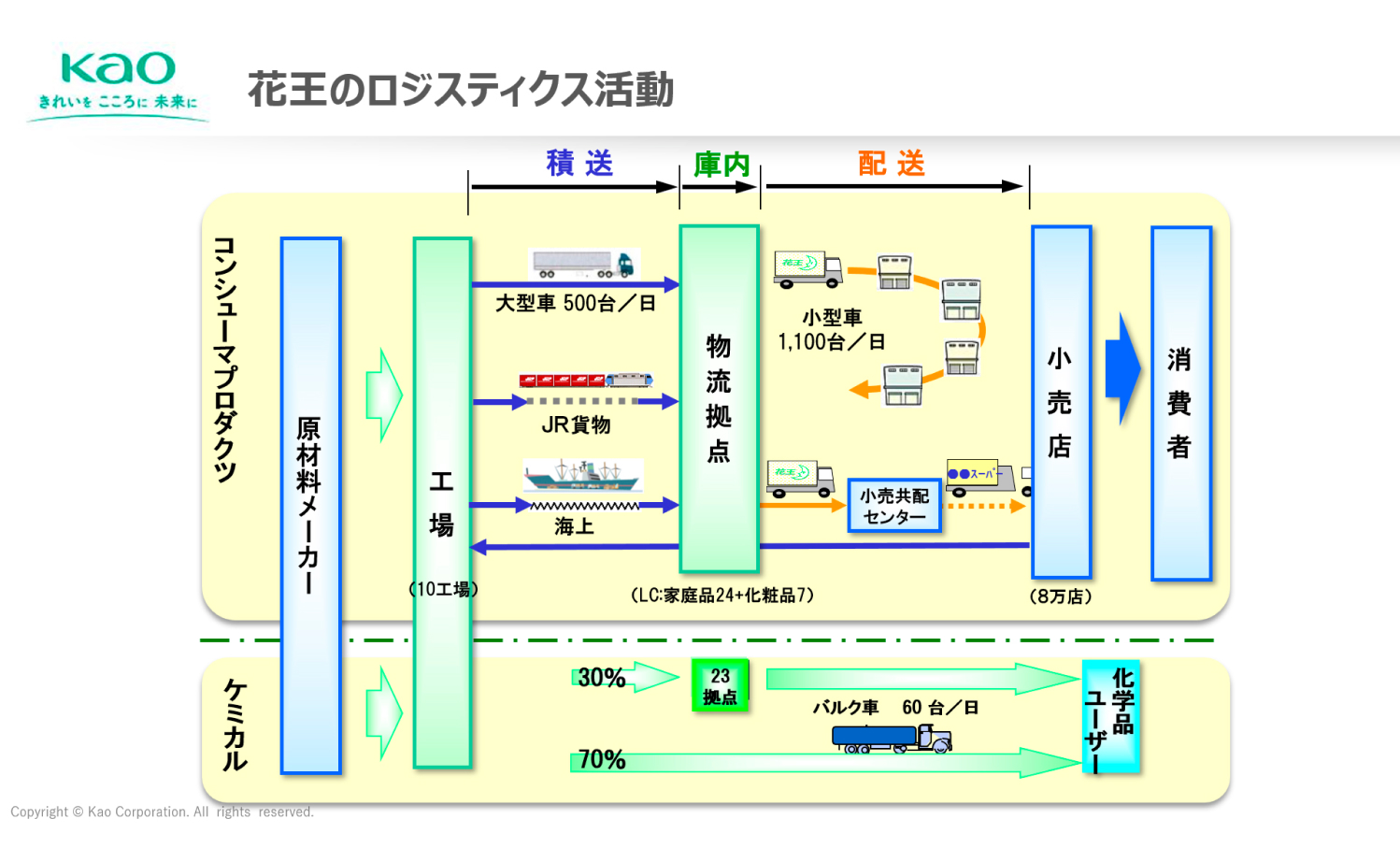
1つ目は、トラック輸送から環境負荷の小さい鉄道や船舶へ輸送モードを転換する「モーダルシフト」です。
花王の生産工場は全国に10拠点あり、そこから全国の物流拠点へ商品を届ける必要があります。近年特に力を入れているのが海路活用です。実際に、和歌山工場から千葉のロジスティックスセンター間の輸送としてRORO船(※1)を利用した海上輸送を始め、陸路での距離約600㎞のトラック輸送を無人化しています。また、船を使用することで、トラックが排出するはずだったCO2の削減にも繋がっています。
※1:RORO船…公共の物流専用船
青木 金銭的なコストでみれば、距離が短い場合は海上輸送の方が高くなりますが、長距離になればなるほど海上輸送の方が安くなります。また、コストの面以外においても、トラックによる長距離輸送を抑制することができ、2024年問題にも関係するドライバーの時間外労働時間を削減し、働き方を改善することができます。トラック輸送に比べると海上輸送では港湾での荷役作業等が必要なため、リードタイムの増加が発生するデメリットはありますが、全体最適を検討して海上輸送の活用を進めています。
徳山 通常リードタイムが伸びると在庫への影響が懸念されます。しかし、花王では生産から販売までのデータを広くとらえているため、商品ごとの販売予測から全国の物流拠点の在庫を設計しており、それに基づいた供給計画を立案しております。これにより欠品は抑制しつつ、在庫量増加の懸念を軽減させながらモーダルシフト化を行うことができます。
徳山
2つ目のアプローチが「トラックドライバーの生産性向上」です。
これは輸送以外の時間をしっかり削減し運行効率をあげることや、花王だけでなく他社と共同で輸送をすることで、積載率を向上させるなどの活動です。
過去の事例として、当社と競合他社でそれぞれの幹線輸送の「帰り便の活用」を行った共同輸送の取り組みもありました。
競合他社との共同輸送とは驚きですね。
徳山 商流においては競争がありますが、「物流は協調領域である」と考えています。物流の2024年問題は個社による対応では限界がありますので、業界をリードして共同物流を推進していきたいと考えています。
サプライチェーン変革に向け、豊橋工場のプロジェクトを開始
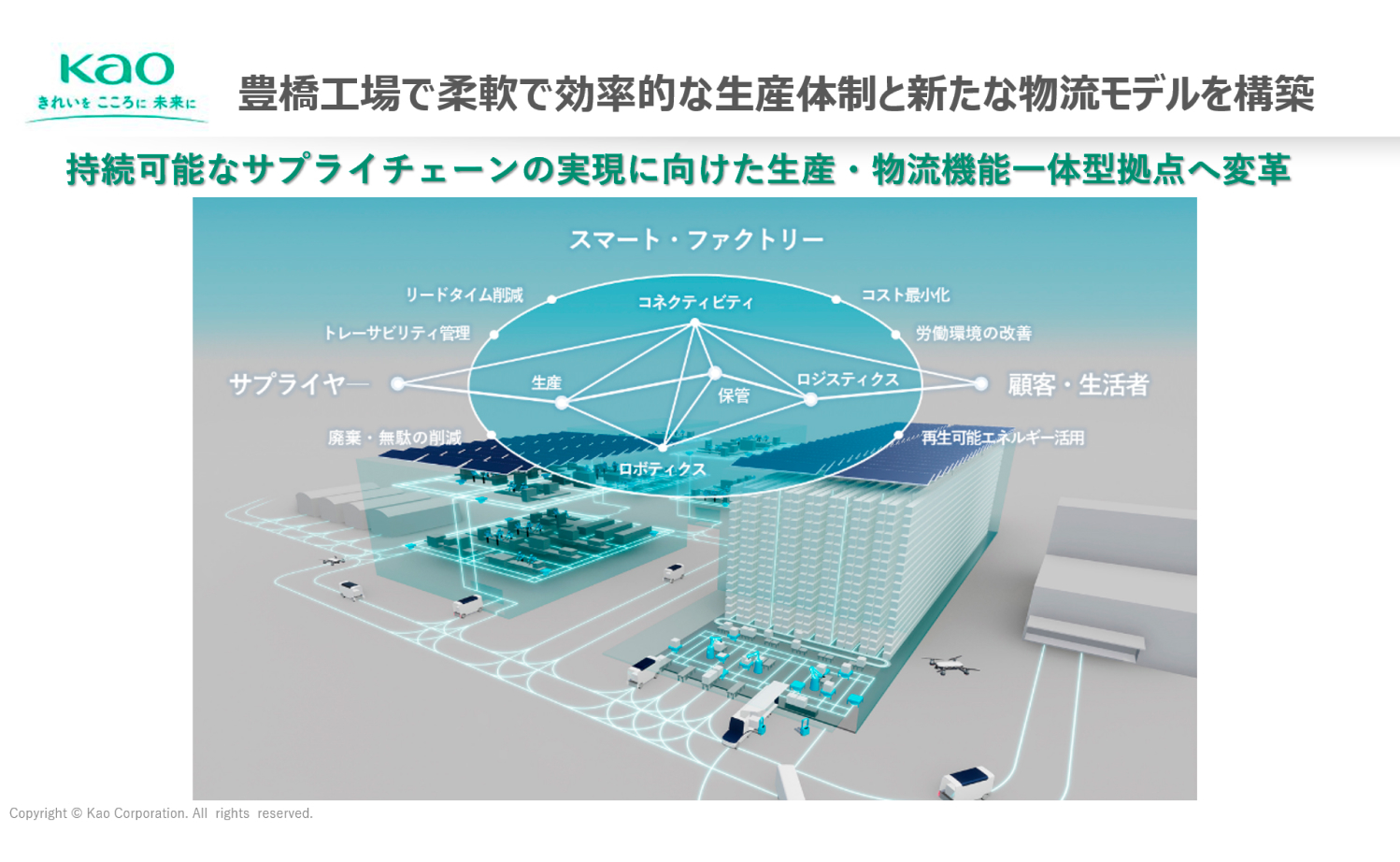
リンク:<花王ニュースリリース>「豊橋工場に次世代新倉庫が完成」(2023年3月27日)
では次に、徳山様、青木様が参加した花王豊橋スマート倉庫プロジェクトについてお聞かせください。
徳山 ビオレやニベアなど、スキンケアやヘアケア製品の供給拠点である豊橋工場の特徴は「少量多品種生産」です。これまで柔軟で効率的な生産体制を構築してきましたが、新たな物流モデルとして「コネクテッド・フレキシブル・ファクトリー」というコンセプトのもと豊橋工場を生産・物流機能一体型の拠点へ変革させる取り組みを開始。その中心として、工場内に完全自動化した次世代新倉庫を建設するプロジェクトが発足しました。それが「花王豊橋スマート倉庫プロジェクト(略称KTS)」です。
KTSプロジェクトではどのようなことに取り組まれたのでしょうか。
徳山 プロジェクトは2020年9月にスタートしました。私はこのプロジェクトのPMO(プロジェクトマネジメントオフィス)兼運営チームリーダーで、青木は運営チームメンバーの一員として、輸送に関わるトラックのオペレーションの最適化を担当していました。プロジェクトの発足と同時に我々のチームの目指すべき姿のひとつとして、「トラックが入ってくるところから出ていくところまで無人化でオペレーションできないか」という「場内トラック運行のスマート化」構想を開始しました。
システム連携で車両入退場の自動化と無人化を実現
「場内トラック運行のスマート化」に取り組まれた背景を教えてください。
徳山「倉庫の無人化」が当初からコンセプトにありましたが、倉庫内に自動化設備を導入するだけでなく、トラックが待機なく効率的に輸送できるようにしたいと考えました。最初に行ったのは、現状の運用の調査と現場へのヒアリングです。そこで分かったのは、トラックが入場して退場するまでには、いくつかの作業工程があり、それぞれに作業時間や待機時間の発生要因があったりすることや、オペレーション自体が人手による紙を使ったアナログなものが多いことでした。これらを解消するためにトラック運行のスマート化が必要と考えました。
現場の課題を聞いて検討を開始したのですね。
では「場内トラック運行のスマート化」の実現をどのように進めたのでしょうか。
青木
以前から、Hacobu社のバース予約受付システム(※2)「MOVO Berth(ムーボ・バース)」の花王倉庫への導入を私が担当しており、MOVO Berthを活用してトラック入退場管理の無人化が実現できないかと考えていました。世の中にあるソリューション調査のため展示会に出向いた際に、JKPIの車両ナンバー認証システムを知りました。ヒアリングを行ったところ、JKPIがHacobu社とも情報交換をしていること、また、同じ将来像を持っていることから、車両ナンバー認証システムとMOVO Berthを連携させて入退場を自動化できるのではと考え始めました。他社の製品も比較検討を行いましたが、機能要件とコスト面において満足できるシステムであり、そして何よりお互いが取り組みたいという想いがマッチしていたことから、JKPI、Hacobu社と共に無人化構想の実現に向けた取り組みを開始しました。
※2:トラック荷物の積み降ろしのためにトラックを停車する場所(バース)の予約管理を行うシステム。
徳山 プロジェクトキックオフ後、さまざまな将来構想の具体的検討を進めていた時期にシステム間を連携した仕組みの検討を開始しました。「ここのトラックって1日何台来るのだろうか」、「こんな時間に来るよね」といったことや、トラックが入ってきたときにどのようにして入退場の管理をするか、限られたバースの中でどのような時間、順番で積み込むのかなど、現場の目線になってディスカッションを重ねました。現地の物流センターの所長をはじめとした実際の現場のメンバーも運営チームに入って、JKPIと共に検討を重ねて、今回のアイデアが生まれました。
トラック入出場管理を無人化するために行った連携システムとはどのようなものなのでしょうか。
徳山 トラック入退場時の「車両ナンバー認証システム」、「バース予約システム」、「出庫システム」を連携した車両入退場スマート化システムを開発しました。
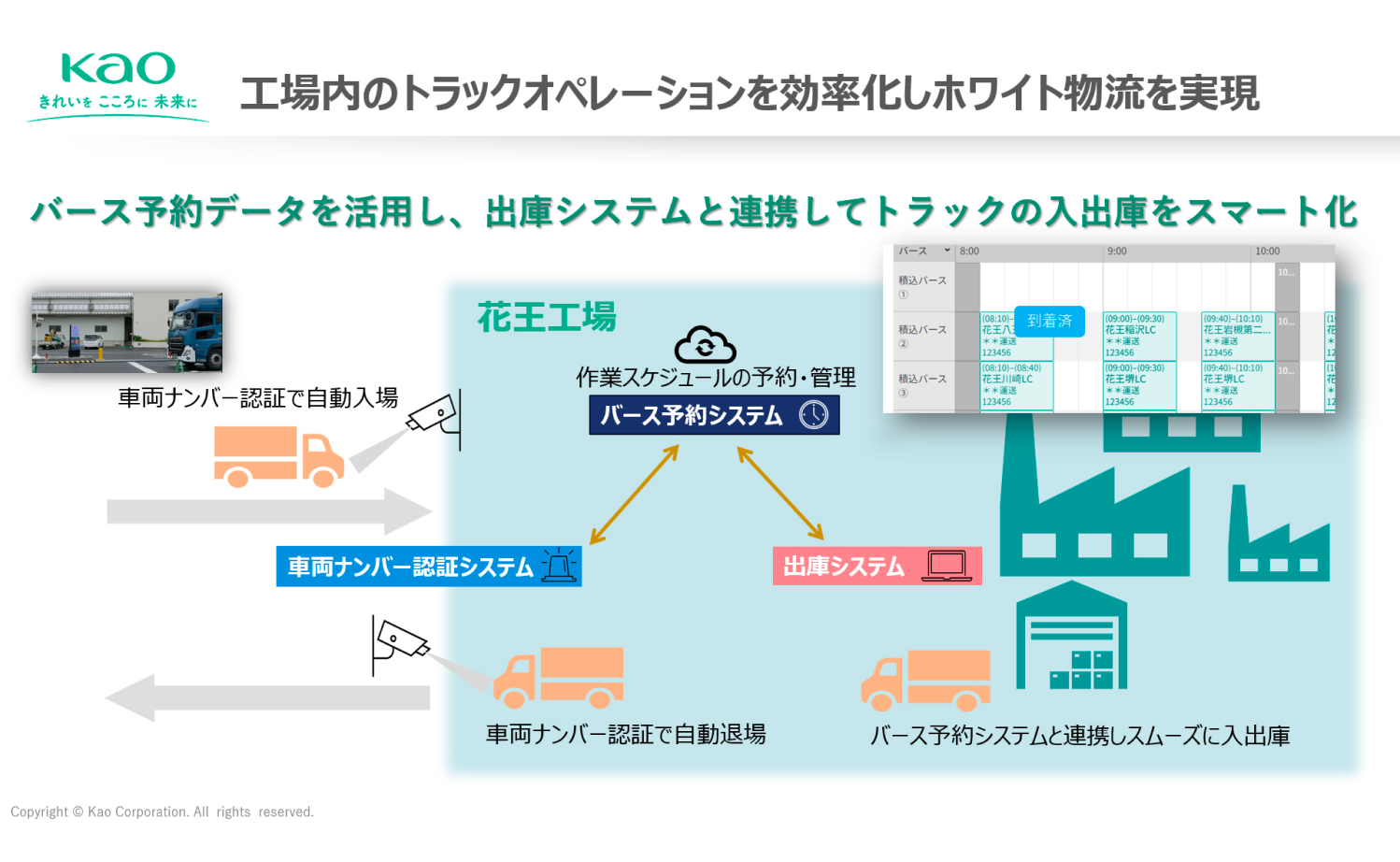
Hacobu社のMOVO Berthは混雑回避を目的とした車両作業時間が予約できるシステムです。我々はここに車両ナンバー認証システムを組み合わせることで、入場時に行先を掲示したり、前の車両が作業中で混みあっている場合は一旦待機場所へ案内することが可能となると考えました。そこで、車両入場口にデジタルサイネージを設置し、車両ナンバー認証システムから案内表示が行えるよう、JKPIに開発を依頼しました。
今回の連携で肝になっている「車両ナンバー認証システム」、「バース予約システム」、「出庫システム」は全て既存の仕組みです。汎用的な3つの仕組みをそれぞれ連携して繋げることができたことで、花王の中でも今後横展開ができる可能性があると考えました。また汎用システムの組み合わせなので他の企業様でも導入しやすいものであると思っています。
異なる会社のシステムを連携させるのは難しかったのではないでしょうか。
青木はい、構想で描いた現場の動きに合わせ、異なる3つのシステムをリアルタイムに連携させる仕組みの構築には苦労しました。倉庫には物流車両以外の車両が出入りすることもあります。入退場する車両を分類し、分類ごとに正しいメッセージを掲示させるため現場のフローとシステムのフローを細かく設計、検討を重ねました。その結果、車両の到着を車両ナンバー認証システムで認証すると、それをトリガーにして自動倉庫から車両荷物が自動で出庫され、さらにドライバーに対して「何番バースにお越しください」と表示を出すことができる仕組みになりました。
また、困難を極めたのはシステムのセキュリティ面です。バース予約システムのようなインターネット接続が必要なクラウドアプリや車両ナンバー認証システムのような外部システムと、倉庫の制御系のシステムをリアルタイムにデータ連携させることは、社内でも前例が無く、セキュリティを担保しつつ直接設備が動くデータと社外のシステムとの連携を実現できる方法を、情報システム部門や関連部門を巻き込んで議論を重ね、実現に至りました。
ドライバー案内用のデジタルサイネージについては検証を重ねたと伺いました。
青木サイネージの大きさや設置場所にはこだわりました。関係する車両の動線を考慮し、どのような入退場動線が適切かを、実際に現場を観察しながら検討したり、サイネージに表示するフォントのサイズを確認するために実際のトラックの助手席に乗車し視認性を確認したりしました。サイネージの表示サイズや発色の具合についても実機で確認しました。また、入退場時の車両ナンバーを読み取るために最適なカメラの位置や設置場所を決めるため、JKPIに現地へ来ていただき仮設をして検証を行いました。
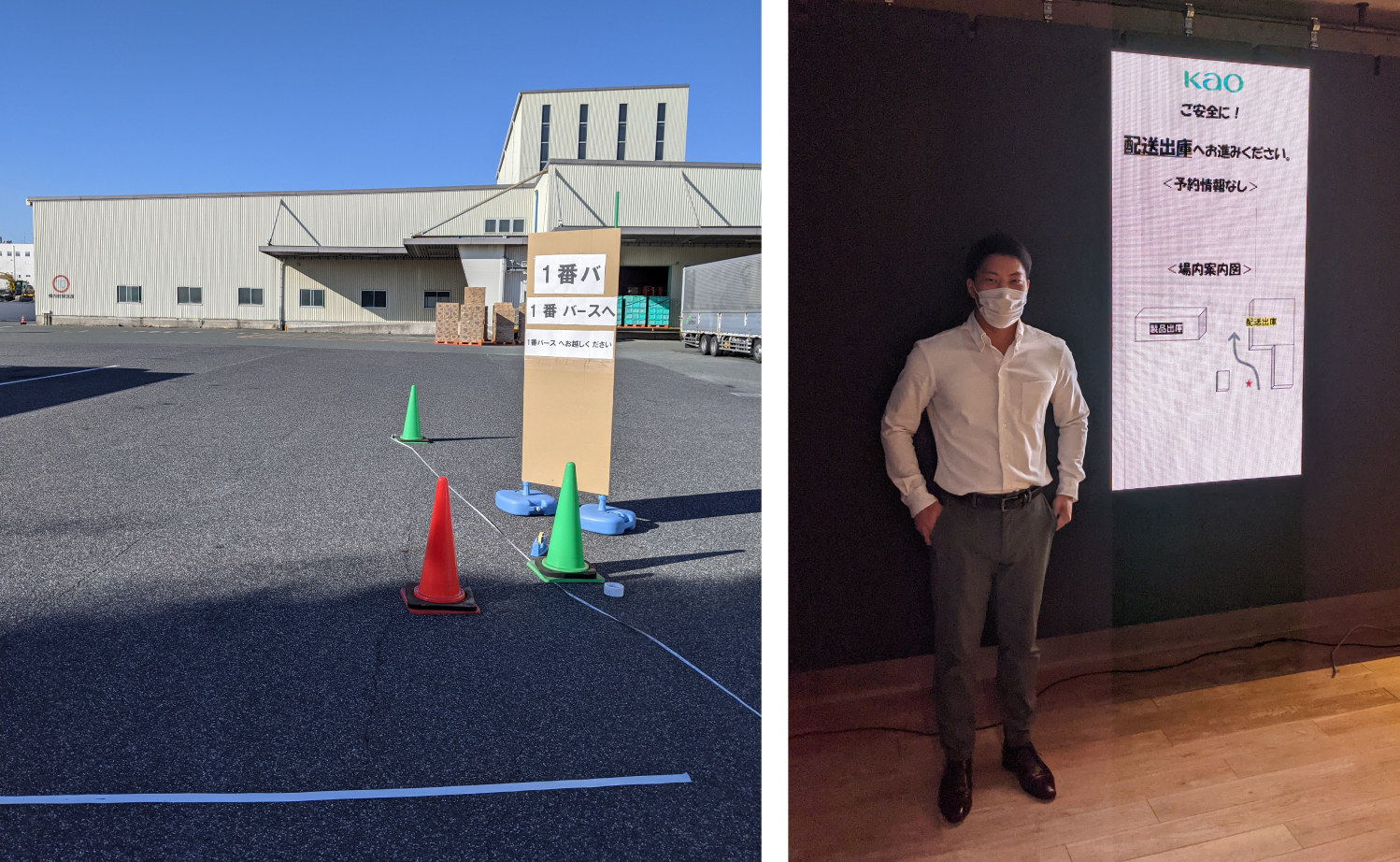
運用ではドライバーの方の協力も必要と思いますが、苦労された点はありますか。
青木 課題となったのがドライバーへの指示です。無人化オペレーションであるため、車が入って来るタイミングでドライバーに分かりやすいように案内を行わなければいけません。ドライバーがしっかりサイネージを確認できる仕組みや無人化されたオペレーションの構築ができるまではやはり難しかったですね。
徳山 運送会社にはシステムを導入する前から協力いただきました。今回導入した仕組みは運送会社がバース予約システムへの入力が必要ですが、入力方法についても青木や関係部門の担当者が運送会社の責任者を集めて説明会を開き理解を深めていただきました。稼働後もコミュニケーションをとるために運送会社の責任者が頻繁に現場に足を運んでくれていました。現在は入力ミスもほぼなく、「この倉庫に携われて良かった」というお言葉までいただいています。
システムの導入効果はいかがでしょうか。
青木
トラック入出場管理を無人化することで、従来のやり方だと必要になるはずであった受付専用担当者の業務が無くなり、他の忙しい業務に回ってもらうことができるようになりました。また、受付は電子データとして自動で記録されるので、システムへの入力ミス等も無く、紙ベースの受付表も不要となりました。
併せて一番の目標としていた待機時間の削減については、現在では殆ど待機時間がなく運用ができている状態になっています。また、国土交通省などが策定したガイドラインにも記載がありますが、トラックの入場から退場までの時間の記録をこの仕組みでしっかりと管理できています。ドライバーだけでなく、我々としてもシームレスに自動で入退場の記録が取得できているので、管理面でもストレスがありません。
「場内トラック運行のスマート化」は無事に目標を達成したということですね。
では、KTSプロジェクト全体についての評価はいかがだったでしょうか。
徳山設計当初に掲げていた目標数値はほぼクリアできました。プロジェクトがクローズしてからも、社内外で多くの反応や問い合わせをいただいています。
青木ドライバーからとても好評をいただいており、「新しい倉庫でロボットが荷物を作っているらしい」と興味を持っていただいているようです。もともとドライバーを強く意識していて、綿密なコミュニケーションを取りながら設計したため、「決まった時間に行けばすぐ積み込み開始できる」と認識いただけたのは大変嬉しく感じています。また光栄なことに、この豊橋工場の次世代倉庫は稼働後多くのメディアや企業様からの問い合わせがあり、1つの理想的なモデルとして興味を持っていただいています。ドライバーにも取材に対応いただくなど、現場作業者のモチベーション向上にも繋がりながら、日々稼働をしています。
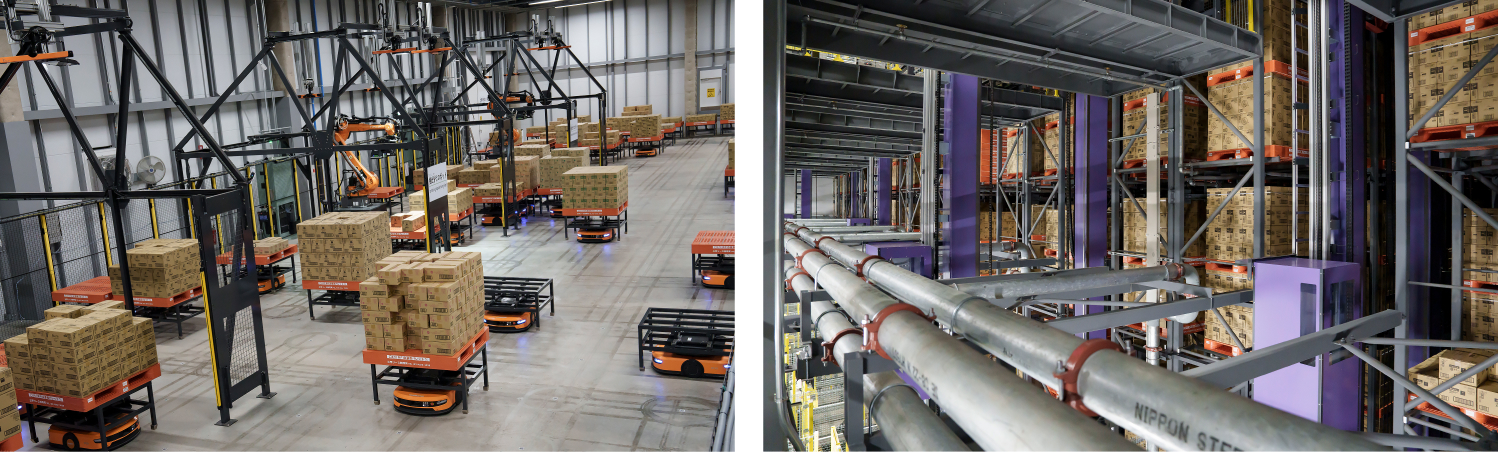
汎用システムを活用したKTSプロジェクトの取り組みは、他工場や拠点への展開を既に考えられているのでしょうか。
徳山これまでの拠点では、固定設備が多く品種数の増加などの環境変化への対応が難しく、結果的に人手による運用でカバーをしているケースもありました。今回の倉庫は固定設備を極力なくし、汎用性・拡張性のある設備・システムにしたため、今後の物流モデルの1つとして、入退場のスマート化や重労働作業の無人化など機能ごとに新規拠点や既存拠点へ展開できるものとなっています。現在、各機能単位で必要性の高い拠点から具体的に導入検討を進めています。
サステナブルなコネクテッドロジスティクスの実現に向けて
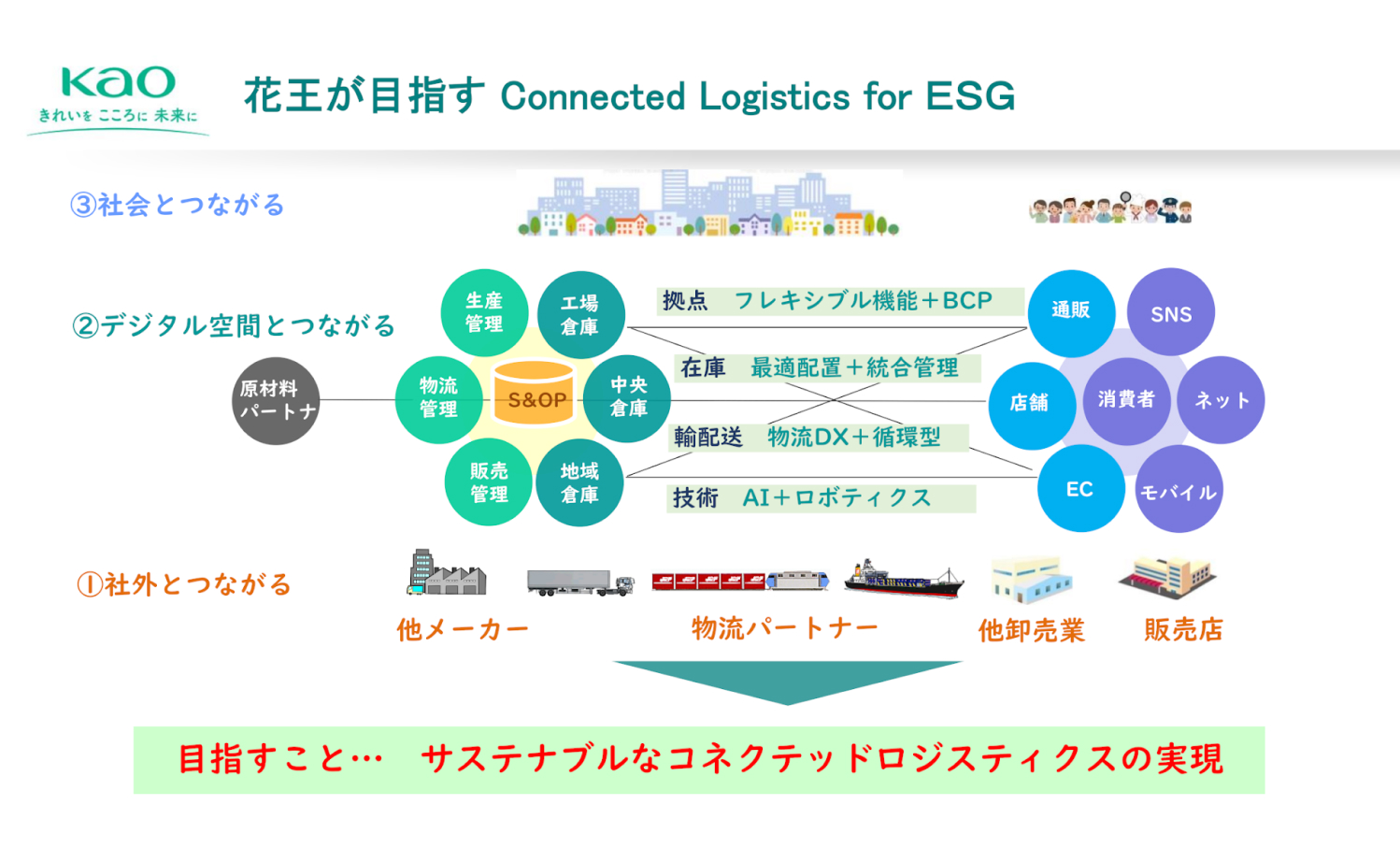
では最後に花王が目指すロジスティクスの姿について今後の展望をお聞かせください。
徳山物流2024年問題はここからが本番だと考えています。規制に対して受け身になるというより、積極的に効率化や解決を進めていきたいと考えています。あわせてサステナブルな物流の実現、DXの推進ですね。今回のような事例を今後も続けていき、物流を止めない取り組みを進めていきたいです。また、こういった取り組みについて、業界を超えて広く活用していただけるような事例を作れたらと考えています。当社工場では見学も行えるようになっておりますので、活動を広く知っていただければと思っております。
我々は「物流は協調領域」だと考えています。広く企業様と協力し合える関係を構築しながら、新しい知見を共有したいと考えています。
青木このプロジェクトで印象に残っていることは、関係各社のモチベーションです。皆の目標が合致したことで、各社が持っている既存のソリューションの範囲にとどまらず、お互い良い方向でシステムをブラッシュアップ、レベルアップできたと感じています。SCMの改善は当社だけではできないことがたくさんあります。引き続き、お互い協力し合って強みを活かし、世の中に貢献できるようなソリューションを共に作っていきたいです。そして、物流やサプライチェーンをより最適化していけたらと考えています。
コネクテッドロジスティクスにもある通り、今後は輸送面の共同化を進めていきたいと考えています。当社は、現場輸送のノウハウを持ちつつ、しかしオリジナルに留まらず、強みを持った他社と協調しながらより良い物流環境を共創していきたいと考えています。特に私はデータを活用した効率化の検討を行っているので、データでどのように繋がっていくかを日々考えているところです。今後のドライバー不足や人手不足などに対し、データ・最新システムを活用して効率化・自動化を図っていくことで、持続可能なサプライチェーンを構築していきたいと考えています。
本日はありがとうございました。
インタビューを終えて
物流業界に顕在している諸課題の解決に向けて、業界に先駆けて自動化・効率化の取り組みを推進している花王様。前例のない仕組みを生み出す大変さや、プロジェクトへの熱量は想像を超えるものでした。
今回、繰り返しお話ししていた共創というキーワードが特に印象に残っています。
業界全体を変化させるために、先駆者として自社技術をもオープンにして働きかけていく姿勢に感銘を受けるとともに、ホワイト物流やカーボンニュートラルの実現は一社一社の意識と取り組みが不可欠であることを強く再認識させられるインタビューとなりました。