コラム
荷待ち時間とは? 法令やガイドライン、改善策も含めて紹介
2025年4月22日
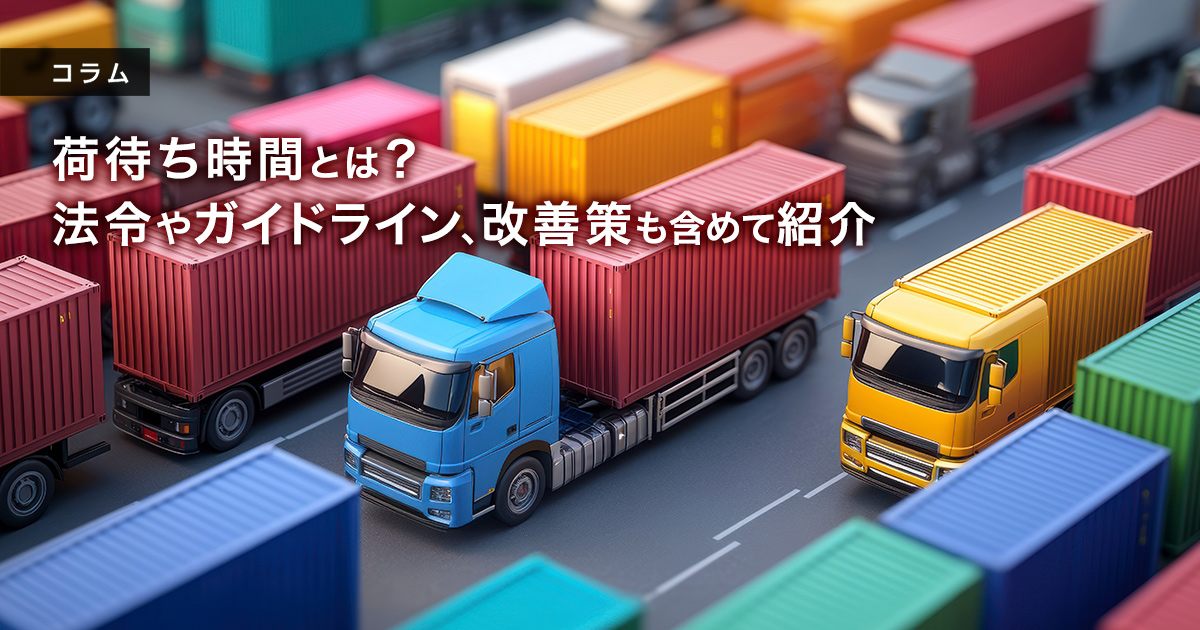
日本の物流を支えるトラックドライバーにとって、積み込み先や荷下ろし先での「荷待ち時間」は深刻な課題です。そんな物流機能を維持するために、国や業界が一丸となってガイドラインを策定し、荷待ち時間の削減に取り組む動きが加速しています。
本記事では、最新のガイドラインや具体的な改善策、そして荷待ち時間をめぐる法規制のポイントを分かりやすく紹介します。
目次
- 1 - 荷待ち時間とは?
- 2 - 荷待ち時間に関する最新のガイドライン
- 荷待ち時間に関連するガイドラインの概要
- 2時間ルールとは
- 働き方改革関連法による影響
- 労働基準法の適用範囲と注意点
- 3 - 荷待ち時間が発生する主な原因
- 荷主との連携不足
- 不適切なスケジューリング
- 交通状況
- システムやツールの未整備
- リスク発生時の対応策の未整備
- 4 - 荷待ち時間改善のための具体策
- スケジューリングの見直しと最適化
- 最新技術を活用した効率化
- 荷主との連携強化
- ドライバーへの適切な指導と教育
- 荷待ち時間の改善事例
- 5 - 荷待ち時間について業務担当者が知るべきポイント
- 補助金の活用について
- 荷主が抑えておくべきポイント
- 運送業が抑えておくべきポイント
- 倉庫業が抑えておくべきポイント
- 6 - まとめ
1 - 荷待ち時間とは?
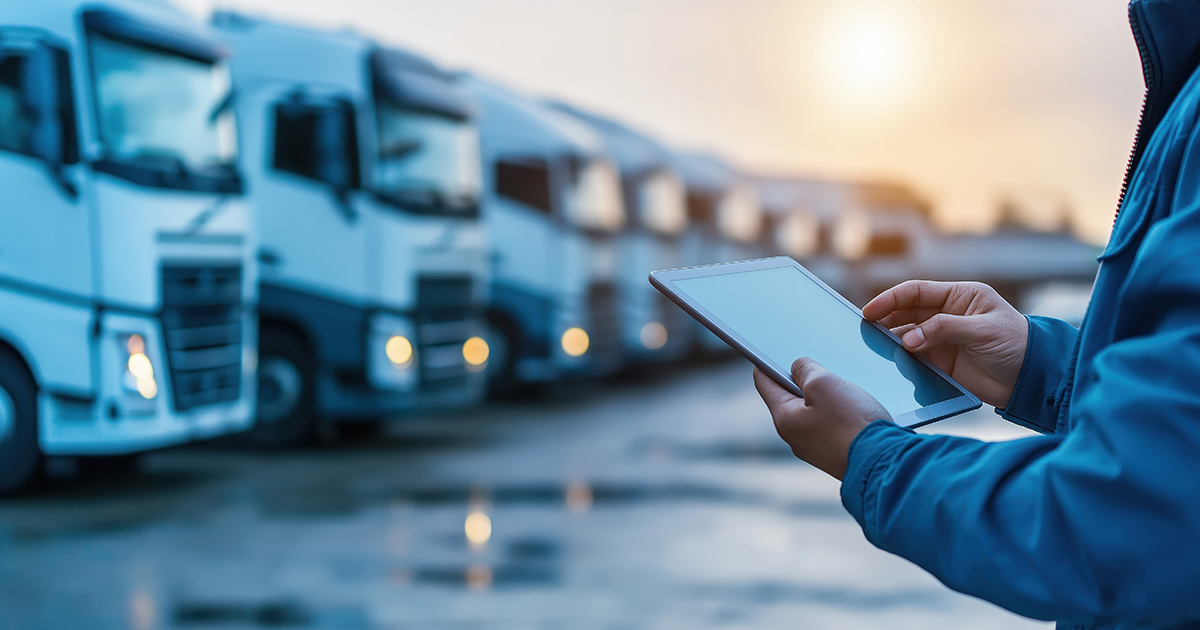
「荷待ち時間」とは、トラックドライバーが荷物の積み込み先や荷下ろし先の物流拠点で順番待ちのために待機している時間のことです。
この荷待ち時間はドライバーにとって無駄な待機であり、日本の物流現場で長年当たり前のように存在してきた大きな課題です。近年では深刻化するトラックドライバー不足の中で、ドライバーの長時間労働を是正し物流機能を維持する必要性が高まっており、官民を挙げて荷待ち時間削減に向けた取り組みが進められています。
2 - 荷待ち時間に関する最新のガイドライン
ここでは、荷待ち時間の問題を解決するために設定されているガイドラインについて紹介します。
荷待ち時間に関連するガイドラインの概要
深刻なドライバー不足と2024年からの労働規制強化(いわゆる「2024年問題」)を背景に、政府は荷待ち時間問題の解消に向けた包括的な施策を打ち出しています。
2023年6月、国土交通省・経済産業省・農林水産省の3省は共同で「物流の適正化・生産性向上に向けた荷主事業者・物流事業者の取組に関するガイドライン」(以下、物流ガイドライン)を策定しました。
このガイドラインは、トラック輸送力不足の懸念に対応しつつ物流の生産性を向上させることを目的に、発荷主(荷物を発送する側)、着荷主(荷物を受け取る側)、そして物流事業者それぞれが取り組むべき施策を示したものです。
物流ガイドラインの中では、荷待ち時間や荷役時間の削減が重要項目として挙げられています。大手企業を中心に業界・分野別の自主行動計画を策定し、早期に具体的な取り組みを進めることが求められており、荷主・物流事業者間の連携強化によって物流全体の効率化を図る方針が示されています。つまり、このガイドラインは単に政府からのお願いではなく、関係各所が一丸となって荷待ち問題の改善に取り組むための指針となっています。
2時間ルールとは
物流ガイドラインで特に注目されているのが「荷待ち・荷役作業時間合計2時間以内ルール」です。これは荷主側に対し、トラックドライバーの荷待ち時間と荷役作業時間を合わせて原則2時間以内に収めるよう求める基準です。
すでに通常から待機+荷役が2時間以内に収まっている荷主については、さらなる短縮目標として1時間以内を目指すことも盛り込まれました。
この2時間ルール自体は法律で厳罰を伴うものではなくあくまで目安ですが、数値目標を明示することで荷主に適切な時間管理を促す効果が期待されています。
具体的には、国土交通省の調査による1運行あたり平均的な荷待ち時間1時間34分と荷役時間1時間29分(合計約3時間3分)という現状を、まずは2時間以内に短縮しようというものです。これにより、2024年度に予測される約14.2%の輸送力不足のうち、4.5ポイント分を創出できると試算されています。この「2時間以内」という指標は、荷主・倉庫・運送会社間で共通認識とすべき新たなサービス水準と言えるでしょう。
働き方改革関連法による影響
働き方改革関連法の施行により、トラックドライバーの労働時間管理も大きく変わりました。2024年4月1日から自動車運転業務にも時間外労働の上限規制が適用され、トラックドライバーは年間960時間までという上限を守る必要があります。
これまでは自動車運転者は他業種より規制が緩和されていましたが、5年間の猶予期間を経ていよいよ一般の上限規制が適用された形です。その結果、1日あたり原則13時間を超える拘束時間の運行は認められなくなり、年間では3,300時間・月間では284時間という拘束時間の総量規制も加わりました。
労働基準法の適用範囲と注意点
荷待ち時間を語る上で、労働基準法上の労働時間の考え方を理解することも重要です。労基法における「労働時間」とは、「使用者(会社)の指揮命令下に置かれている時間」を指します。この定義に照らせば、ドライバーが荷役開始を待っている荷待ち時間は基本的に「労働時間」とみなすべきものです。
例えば「積み下ろしの開始時刻がまだ決まっておらず、いつ呼ばれるか分からないからトラックから離れられない」といった状況での待機は休憩ではなく労働に当たります。
逆に、明確に荷役開始時刻が決まっていてそれまで自由に過ごせる場合などは例外的に休憩と認められる可能性がありますが、実務上は判断が難しいため慎重な対応が必要でしょう。
また、2017年以降は一定以上の荷待ち発生時の乗務記録作成が義務化され、違反すれば行政処分の対象ともなります。ドライバーが自社社員であるか請負契約かにかかわらず、労務管理上は拘束時間・荷待ち時間を正確に把握し、法定範囲に収めることが求められます。「荷待ち時間=休憩ではなく労働」である点を社内外で周知徹底し、荷主との契約や運行計画にも織り込んでいくことが重要です。
3 - 荷待ち時間が発生する主な原因
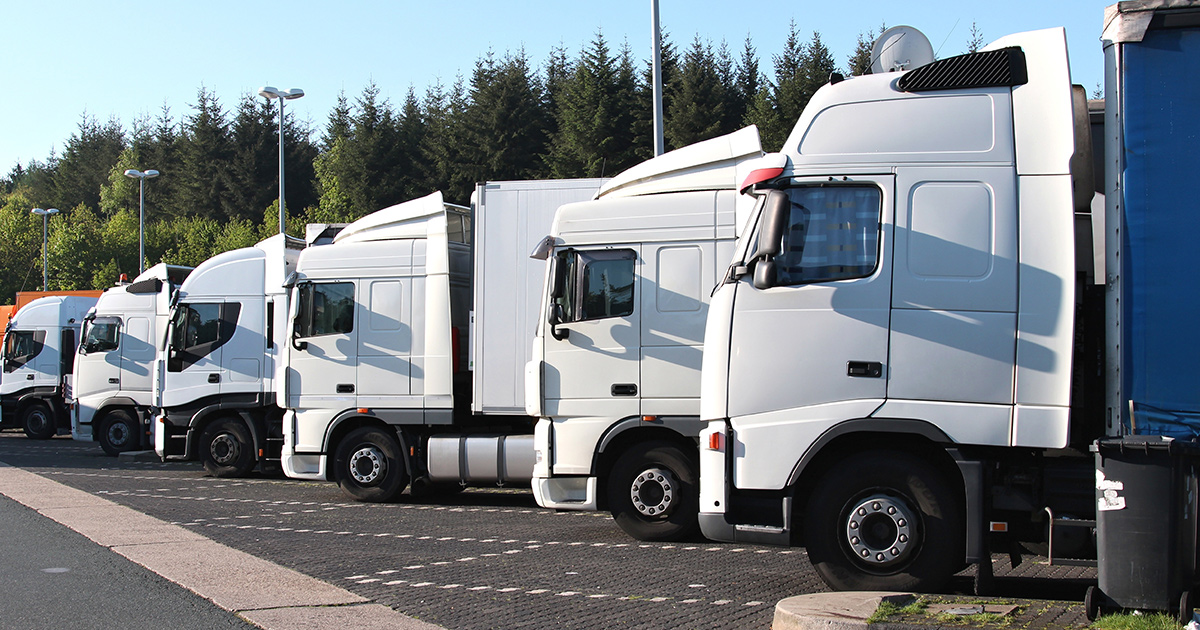
荷待ち時間の改善に向けて、荷待ち時間が発生する原因を理解することも大切です。ここでは荷待ち時間が発生してしまう主な原因を5つ紹介します。
荷主との連携不足
荷主(荷物の発送元・受取先)と運送事業者との連携が不十分だと、荷待ち時間が長引く大きな要因となります。現状では、荷主側が自社の物流現場でどの程度トラックを待たせているか把握していないケースも多いです。
国土交通省の調査によれば、運送会社側では約73%が「荷待ち時間が発生している」と認識しているのに対し、元請では約55%、発荷主では約20%しか荷待ち時間の発生を認識していません。荷待ち時間に対する認識ギャップがあると、荷主は待機削減の必要性を感じづらく改善に消極的になりがちです。結果として運送会社任せで効率化が進まず、いつまでも長時間待機の慣行が是正されない原因となっています。
不適切なスケジューリング
トラックの配車計画や配送スケジュールの組み方自体にも、荷待ち時間を発生させる要因が潜んでいます。非効率なスケジューリングとは、言い換えれば「物流プロセスにおけるタイミングの不整合」です。
例えば多くの荷主が午前中指定で配送時間を設定すると、その時間帯にトラックが一斉に集中してしまい、結局どのトラックも順番待ちで待機することになります。このように受付時間が特定の時間帯に重なり過ぎると、現場の処理能力を超えてしまい待機列が発生します。
交通状況
道路の交通状況も荷待ち時間に影響を与える主要因の一つです。トラックは長距離輸送や都市部での配送において渋滞や交通事故による遅延リスクを常に抱えています。計画通りに現地に到着できない場合、後続のスケジュールが崩れ物流施設で待機する時間が発生します。
また、ドライバー側の判断で納品先付近に早く着きすぎてしまうこともあります。渋滞を見越して早めに出発した結果、予定より相当早く到着してしまい、指定時間まで施設の外で待たざるを得ないといったケースです。このように交通事情と運行計画のズレによっても荷待ち時間は生じます。
システムやツールの未整備
ITシステムの導入・活用不足も、荷待ち時間問題を長引かせる大きな原因と考えられています。物流現場では未だに電話や紙ベースでの調整、現場担当者の経験に頼った管理が行われている状況も少なくありません。
IT化が進んでいないと「今どの車がどれだけ待っているか」「次にどの荷物を準備すべきか」といった情報がリアルタイムで共有されず、結果的に無駄な待機や手持ち時間が発生します。逆に言えば、適切なシステムを整備すれば防げる待機が見過ごされてしまっているのです。
リスク発生時の対応策の未整備
物流現場では予定外のトラブルやイレギュラー対応がつきものですが、そのリスク対応策が事前に整備されていないことも長時間の荷待ちを招く原因となります。
具体的には、配送中の事故・故障や天候不良、受取側の急な事情変更など「計画通りにいかない事態」が起きた際に、関係者間でどうリスケジュールし対応するかが決まっていないケースです。
計画外の事態が発生した場合でも、あらかじめ連絡フローや代替案が用意されていればドライバーの待機時間を最小限に抑えることができます。しかし何の取り決めもないまま現場任せになると、対応の手順をゼロから考えねばならず、その間トラックはただ待つしかありません。このようにリスク時のルールがないことは、ドライバーに無駄な待機を強いる結果につながります。
4 - 荷待ち時間改善のための具体策
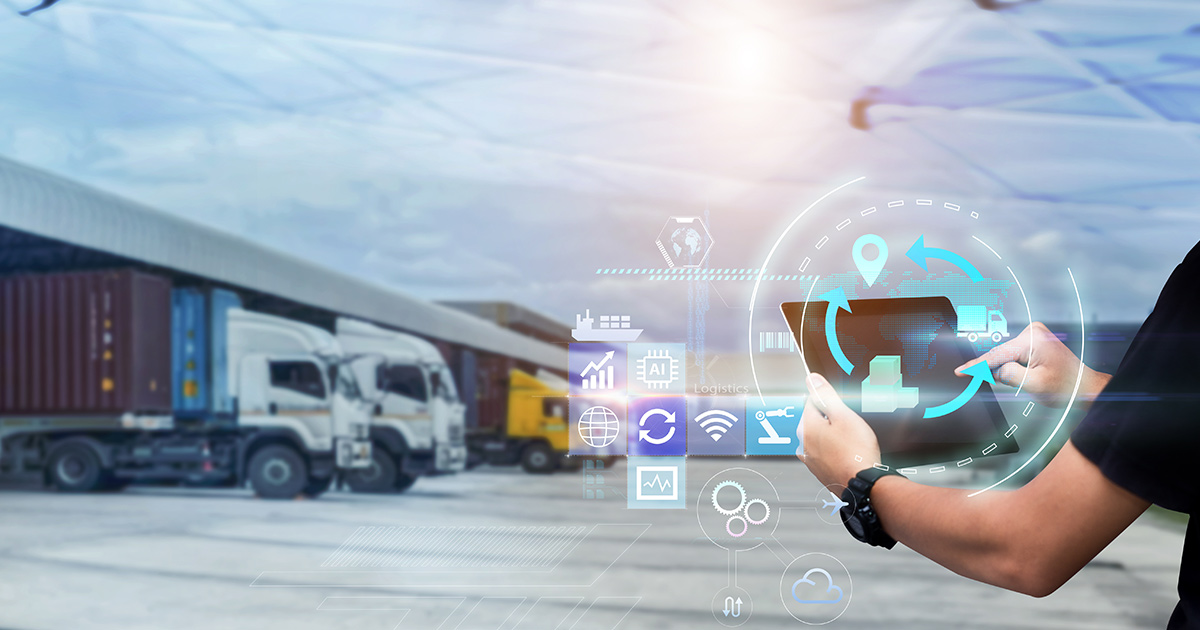
荷待ち発生の原因も踏まえたうえで、続いては荷待ち時間を改善するための具体策を紹介します。
スケジューリングの見直しと最適化
荷待ち時間を削減する最も基本的なアプローチは、配送スケジュールの見直しと最適化です。前述の通り、トラックの到着が特定の時間帯に集中しすぎると待機が発生しやすくなります。そこで、荷主側は積み込み・荷下ろしの時間帯をなるべく分散させ、時間帯ごとの受け入れ台数に上限を設けるなどの工夫が有効です。
具体的には、午前・午後など広めの時間帯指定に切り替えたり、事前予約制でトラックの到着枠をコントロールする方法があります。
さらに、荷待ち時間削減のためには早着・遅着への対策も必要です。ドライバーが極端に早く着きすぎたり、逆に遅れてしまった場合の対応ルールを決めておくと良いでしょう。
例えば早着しそうな際は事前に連絡して時間調整する、逆に遅延時は次のトラックと順番を入れ替えることを検討する、といった柔軟な措置です。こうした取り決めがないと、どちらのケースでも現場で結局「待機」が発生してしまいます。スケジュールはあくまで“計画”なので、当日の状況に応じてダイナミックに修正・最適化する運用も含めて整備することが肝要です。
最新技術を活用した効率化
物流現場の効率化にはテクノロジーの活用が欠かせません。荷待ち時間削減に寄与する最新技術として代表的なのが、トラック予約受付システム(バース予約システム)です。これはウェブ上でトラックの到着予定時刻を事前予約できるシステムで、倉庫管理者はその予約情報を見ながら荷役の準備や人員配置計画を立てられます。
導入効果として、トラックバース(荷役スペース)の混雑を事前に防げることに加え、「どの車が何時に来るか」が可視化されるため荷主側で作業の優先順位付けが可能になります。結果として待機時間そのものの発生リスクを低減でき、ドライバーも予定通りスムーズに積み下ろしを行えるようになります。
他にも、車両ナンバー認証システムも荷待ち時間短縮に貢献します。車両ナンバー認証システムを導入することで、物流拠点への車両入退場記録を自動化することができるため、入退館管理を省力化と、入退場待ちの削減につながります。
また、バース予約システムとの連携も可能なため、自動受付が可能になります。
車両ナンバー認証システムの情報はこちら
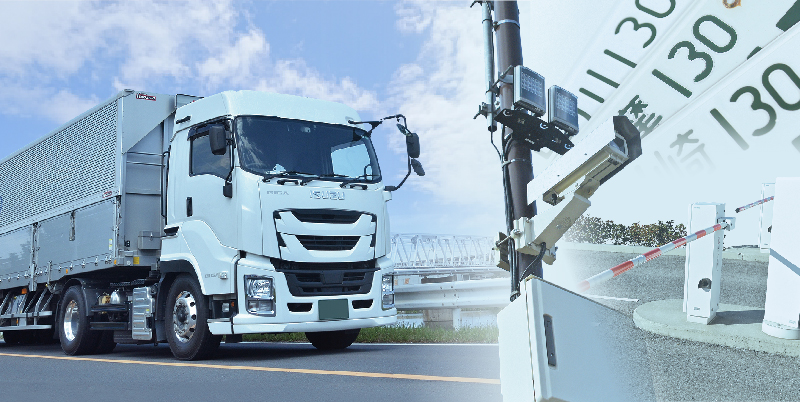
車両ナンバー認証システム
バース予約システムと連携可能な車両ナンバー認証システムを活用した、荷待ち・荷役時間の可視化による物流2024年問題対策をご提案します。
さらに、車両の現在位置や到着予想到達時刻をリアルタイムで共有する車両動態管理システムも有効です。GPS付きの車載端末をトラックに搭載し、運行管理者や荷受け側がオンラインで所在を把握できるようにします。遅延が発生しそうな場合はシステム上にアラートが出たり、ドライバーからの報告を待たずとも関係者全員が状況を把握できるため、早め早めの対応が取れます。
荷主との連携強化
荷待ち問題を解決するためには、荷主側の理解と協力が不可欠です。運送会社だけの努力では限界があり、発荷主・着荷主を含めたサプライチェーン全体での取り組みが求められます。
そのための連携強化策としてまず重要なのは、情報共有の徹底です。配送予定や到着見込み、荷物の準備状況、現場の処理能力などを事前に共有し、予定に変更があれば即座に連絡する仕組みを構築します。具体的には、EDIや物流プラットフォームを通じて荷主と運送会社がリアルタイムに情報交換できるようにしたり、定期的な打ち合わせで課題をすり合わせるといった方法が考えられます。
また、契約面での取り決めも連携強化に有効です。国土交通省は標準的な運送契約のモデルとして「標準運送約款」を定めていますが、2024年の改正では待機時間料の明確化など荷主と運送会社の取引条件適正化が図られました。
荷主にとってはコスト増のリスクが見えるため待機発生を抑制する動機付けとなり、運送会社にとっては泣き寝入りせず正当な対価を得る手段となります。
ドライバーへの適切な指導と教育
現場の主役であるトラックドライバーに対する指導・教育も、荷待ち時間削減の重要なポイントです。まず徹底すべきは、乗務記録への正確な記載と報告です。先述したように30分以上の荷待ちがあれば乗務記録への記載義務がありますが、ドライバーが忙しさに紛れて記録漏れしてしまうと正確な実態把握ができません。
運送会社はドライバーに対し待機発生時の記録・報告を徹底させるよう教育し、運行後には日報やデジタコ記録を確認することが大切です。事実を正確に積み上げることで、荷主への協力要請や経営判断に説得力のあるデータを示せます。
次に、早着・遅着に関する適切な判断を教えることも必要です。真面目なドライバーほど「遅れるといけない」と極端に早く到着しがちですが、前の便が終わっておらず結果として長時間待機になっては本末転倒です。むしろ予定より大幅に早く着きそうな場合は途中で休憩を取るなど時間調整し、なるべくちょうどよい時刻に現地入りするよう促します。また、仮に遅延が避けられない場合でも、事前に連絡する習慣を徹底させます。
荷待ち時間の改善事例
車両ナンバー認証システムの導入により、荷待ち時間が短縮された事例をご紹介します。
花王株式会社 豊橋工場では、車両ナンバー認証システムの導入により、入退場ゲートで車両ナンバーを自動認識、事前登録された情報と照合することで、入退場管理を効率化しています。さらに、バース予約システムと連携し、予約状況に応じた案内をサイネージに表示することで、受付・誘導のオペレーションを無人化しました。
この結果、入場から退場までの在場時間が可視化されるとともに、自動倉庫との連携や手続きの簡素化により在場時間は1時間以内に短縮、ドライバーの負担も軽減されました。また、案内サイネージの導入により、入退場受付や誘導指示、オペレーションの作業工数が削減されました。
5 - 荷待ち時間について業務担当者が知るべきポイント
最後に、荷待ち時間に関して荷主・運送業者・倉庫業者が抑えておくべきポイントを紹介します。
補助金の活用について
荷待ち時間削減や業務効率化のための設備投資を検討する際は、国の補助金制度を上手に活用するのもポイントです。ただし、トラック運送業者を対象とした補助金制度は2025年4月現在、応募期間が終了しているものもあるため注意が必要です。
- 2025年4月現在、補助金を利用できる制度例
- ・IT導入補助金
・自動点呼機器導入促進助成事業
- 2025年4月現在、応募期間が終了した制度例
- ・働き方改革推進支援助成金
・テールゲートリフターや予約受付システム等の導入支援事業
このように公的支援策は多岐にわたるため、自社が計画する改善策に適合する制度を調べてみる価値があります。補助金や助成金を活用すれば初期コストの負担を抑えられ、経営陣の理解も得やすくなります。物流業界全体の持続可能性確保という観点からも、国は予算措置を講じていますので、ぜひアンテナを高くして情報収集し、有効な制度を積極的に利用してください。
荷主が抑えておくべきポイント
荷主企業(発荷主・着荷主)が特に注意すべきポイントは、自社が原因で発生している荷待ち時間を減らすための主体的な取り組みです。
まず、現状把握が出発点となります。自社の物流拠点で平均どのくらいトラックを待たせているのか、ドライバーからクレームは出ていないか、定量的・定性的な情報を集めましょう。
次に、具体的な改善策を講じることです。荷主は荷待ち時間削減の主導権を握っているとも言えます。例えば、出荷業務のプロセスを見直してトラック到着までに荷物を確実に準備できる体制を整える、人手不足であればフォークリフト増員や作業員の配置を見直すなど、倉庫オペレーションの効率化に投資することが求められます。
さらに、関係者との連携を強化する姿勢も重要です。発荷主であれば着荷主や運送会社と協議し、納品時間帯の調整や共同配送の検討などオープンに議論します。着荷主であれば、納品側の都合も踏まえて受入れ時間帯を融通するなど相互理解に努めます。
最後に、コスト意識の改革も必要でしょう。待機時間を削減すればドライバーの拘束時間が減り、その分運送コスト増加を抑制できます。
たとえ待機削減のために追加の人員やシステム導入コストがかかっても、中長期的には運賃の高騰抑止や安定的な輸送力確保につながります。荷主自身の物流費用を最小化する視点でも、荷待ち時間削減は避けて通れないテーマであることを認識してください。
運送業が抑えておくべきポイント
運送業(トラック運送事業者)の業務担当者が押さえるべきポイントは、自社ドライバーの労働環境を守りつつ、生産性を高める取り組みです。まず前提として、荷待ち時間も含めてドライバーの拘束時間を法令範囲内に収めることは絶対条件です。配車担当者は無理のない計画を立て、改善基準告示の範囲内で運行させる責任があります。
仮に荷待ちが発生して労働時間オーバーのリスクが出てくる場合は、運行を中断して休息を取らせるなど安全最優先の判断を徹底します。ドライバーの適正な労働条件を保証し、過労運転をさせないことは運送会社の社会的責務です。
次に、効率的な配車計画と車両運用を追求しましょう。運送会社にとって荷待ち時間は「本来走って稼げる時間を奪われる」損失であり、収益機会のロスです。待機が長引けば運べる件数が減り残業代など人件費も増えるため、経営面でもマイナスです。したがって、可能な限り待機を減らすよう複数案件のスケジュールを調整し、積載効率の高い運行や時間にゆとりのある段取りを心がけます。
倉庫業が抑えておくべきポイント
倉庫業(物流センター運営者)にとって荷待ち問題は、自社のオペレーション効率と直結する課題です。ポイントは、トラックの受け入れと庫内作業をスムーズに行うための仕組みづくりです。まず心掛けたいのは、必要な人員と設備の適切な配置です。荷役作業のピーク時間帯にフォークリフトや作業スタッフが不足しないよう、シフト計画を最適化します。十分なリソースが投入されていれば、一度に複数台のトラックに並行して対応でき、待機させることなく迅速に荷役を進められます。
次に、庫内作業の効率向上です。倉庫内のレイアウトを見直して動線を短縮したり、ピッキングや検品にかかる時間を削減する工夫を凝らします。例えば出荷準備エリアをトラックバース近くに配置し積み込みを素早く行えるようにする、検品作業を事前にできるものは済ませておく、といった施策です。もし手作業がボトルネックであれば、パレット化や自動化機器の導入も視野に入れます。
倉庫業は荷主と運送会社をつなぐハブとして、荷待ち時間削減の鍵を握る存在です。設備・人員・システムの三位一体で効率化を追求し、現場改善の専門家としての役割を十分に発揮することで、日本の物流全体の生産性向上に貢献できるでしょう。
6 - まとめ
荷待ち時間削減は、日本の物流業界における重要な課題です。
トラックドライバー不足や長時間拘束のリスクを解決するために、国や業界全体で新しいガイドラインが策定され、効率化に向けた取り組みが進められています。
荷待ち時間削減の方法として、当社では「車両ナンバー認証システム」をご提案しています。ぜひご覧ください。
編集:株式会社JVCケンウッド・公共産業システム マーケティング担当(2025年4月)
<参考資料・出典>
「物流の適正化・生産性向上に向けた荷主事業者・物流事業者の取組に関するガイドライン」を策定しました (METI/経済産業省)
自動車運転者の労働時間等の改善のための基準(改善基準告示)|厚生労働省
物流情報局(事業者の皆さまへ) | 自動車運転者の長時間労働改善に向けたポータルサイト
自動車:標準貨物自動車運送約款等の改正について - 国土交通省
※本資料は、公開掲載時点での情報であり、内容の完全性・正確性を保証するものではありません。
※本資料内の文章・画像等の内容の無断転載及び複製等の行為はご遠慮ください。